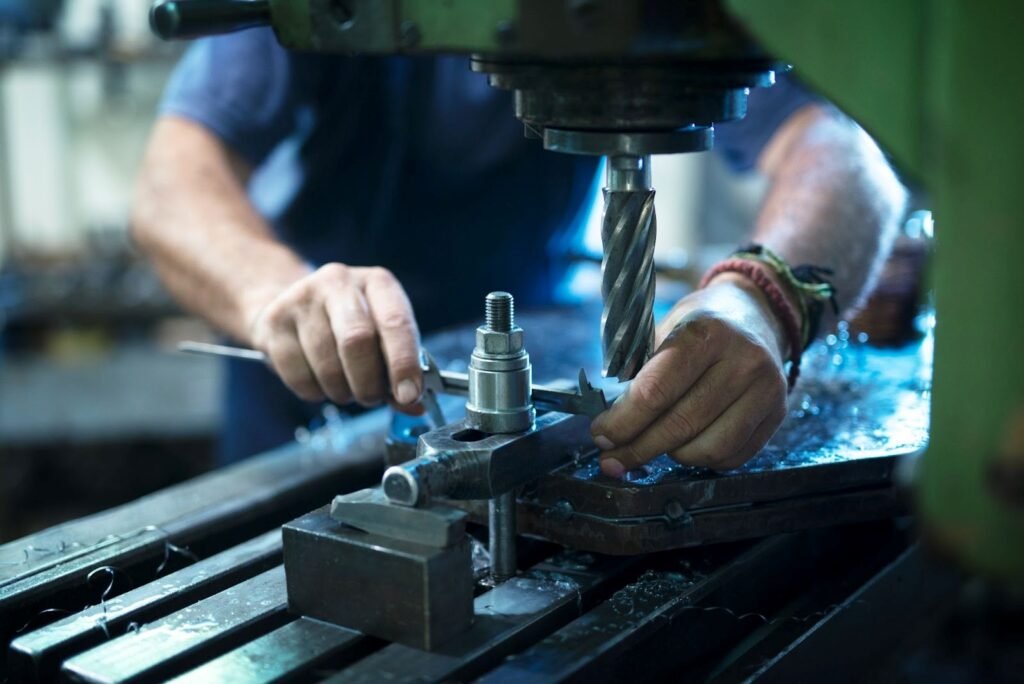
In today’s competitive manufacturing environment, achieving tight tolerances and superior surface finishes is essential for producing high-quality parts and components. Whether you are working on aerospace, automotive, medical, or electronics projects, precision machining plays a crucial role in ensuring that each part fits perfectly within a larger system, functions as intended, and meets stringent industry standards. A precision machining company specializes in using advanced tools and techniques to achieve these exacting standards, and their expertise is invaluable for companies seeking to push the boundaries of design and performance.
In this blog, we will explore how partnering with a company can help you achieve the tight tolerances and superior surface finishes necessary for your most demanding projects. From the importance of precision machining in modern manufacturing to the processes and technologies that enable flawless results, we will take a closer look at how these companies deliver quality and consistency in every component they produce.
The Importance of Tight Tolerances in Manufacturing
Tight tolerances are defined as the allowable variation in the dimensions of a manufactured part. When these tolerances are extremely small, parts must be made with exceptional precision to ensure they fit perfectly with other components. Achieving tight tolerances is especially crucial in industries such as aerospace, automotive, and medical devices, where even the smallest deviation can lead to catastrophic failures or safety issues.
For example, in the aerospace industry, components like turbine blades, engine parts, and landing gear must be made with incredibly tight tolerances. A deviation of just a few microns can result in part failure, affecting the performance, safety, and reliability of the entire aircraft. Similarly, in the medical industry, implants and surgical instruments must be manufactured with precise measurements to ensure they function as intended and do not cause harm to patients.
A precision machining company employs advanced machinery and methods that are specifically designed to achieve these extremely tight tolerances. With state-of-the-art CNC (Computer Numerical Control) machines and expert machinists, these companies can fabricate parts that meet the most exacting specifications, ensuring that each part fits seamlessly within the larger system and performs its intended function.
The Role of Advanced Machinery and Technology
Achieving tight tolerances and superior surface finishes is only possible with the right tools and technology. A company utilizes cutting-edge equipment to produce parts with the highest level of accuracy. CNC machining, for example, is one of the most advanced technologies used in the industry today.
CNC machines allow for highly accurate and automated machining processes. These machines are controlled by computers that interpret a digital design file and translate it into precise machining instructions. This results in a high degree of repeatability, ensuring that each part is made to exact specifications. Additionally, CNC machines can operate with extremely fine tolerances, sometimes as small as 0.001 mm or less, making them perfect for industries that demand precision.
Moreover, modern CNC machines can perform a wide range of operations, including drilling, milling, turning, and grinding. This versatility allows a precision machining company to create complex shapes and intricate features while maintaining tight tolerances. The ability to make adjustments on the fly and monitor the machining process in real-time also ensures that the final product adheres to the required specifications without the risk of errors or inconsistencies.
In addition to CNC machining, other advanced technologies such as laser cutting, EDM (Electrical Discharge Machining), and multi-axis machining are often used to achieve the high-precision results needed for demanding projects. These technologies provide further control over the machining process and allow for greater flexibility in design and production.
Surface Finish Quality: Achieving the Perfect Texture and Smoothness
Surface finish refers to the texture of the surface of a machined part. Depending on the application, parts may require a specific surface finish to ensure optimal performance, aesthetics, and durability. A smooth surface finish may be critical in industries such as aerospace or medical device manufacturing, where the friction or wear of a part can impact performance and longevity.
Achieving a superior surface finish is an essential component of precision machining. A company employs various techniques to ensure that every part is finished to the highest standards. For example, after machining the initial shape of a part, additional processes such as polishing, grinding, and honing are often performed to refine the surface and achieve the desired finish.
Grinding, in particular, is a key technique used to improve the surface finish of parts. It involves using an abrasive wheel to remove material and create a smooth, even surface. Precision grinding machines are capable of achieving surface finishes as fine as Ra 0.1 µm (micrometers), which is ideal for applications where smoothness is crucial.
In addition to grinding, techniques such as bead blasting, anodizing, and electroplating can also be used to improve the surface finish of metal parts. These processes not only enhance the aesthetics of the part but also provide functional benefits, such as increased corrosion resistance or improved wear resistance.
For parts that require an ultra-smooth surface, polishing is often employed. This process involves using a polishing compound and a rotating wheel to remove even the smallest surface imperfections, resulting in a mirror-like finish. The end result is a component that is not only aesthetically pleasing but also resistant to wear, corrosion, and other forms of degradation.
How Precision Machining Companies Ensure Consistent Quality
One of the key advantages of working with a precision machining company is their ability to consistently produce parts that meet stringent quality standards. Achieving tight tolerances and superior surface finishes is not just about using advanced machinery; it also requires a high level of skill and experience from the machinists who operate the equipment.
A company typically employs a team of highly skilled engineers, technicians, and machinists who have extensive experience in the field. These experts understand the complexities of machining and know how to handle different materials, tools, and processes to achieve the best results. In addition, they are trained to use precision measurement instruments, such as micrometers, calipers, and CMMs (Coordinate Measuring Machines), to ensure that every part is within the specified tolerances.
To maintain consistency, precision machining companies often implement strict quality control protocols throughout the production process. From the initial design phase to the final inspection, each step is closely monitored to ensure that all parts meet the required specifications. Any deviations from the desired tolerances or surface finishes are immediately addressed, ensuring that the final product is flawless.
Additionally, many precision machining companies are ISO-certified, meaning they adhere to internationally recognized quality management standards. This certification further ensures that every part produced is of the highest quality and meets the exacting standards required by industries such as aerospace, automotive, and medical devices.
Conclusion:
When working on high-stakes projects that require tight tolerances and superior surface finishes, partnering with a company is a wise choice. These companies bring together advanced machinery, cutting-edge technology, and skilled experts to produce parts with the highest degree of accuracy and quality.
Whether you’re manufacturing aerospace components, medical devices, or automotive parts, a precision machining company can help ensure that your parts meet the most demanding specifications. With their ability to achieve exceptional surface finishes, maintain tight tolerances, and deliver consistent results, these companies are indispensable in modern manufacturing. By leveraging their expertise and technology, you can ensure that your projects are completed with precision, reliability, and excellence.